The Body Shop
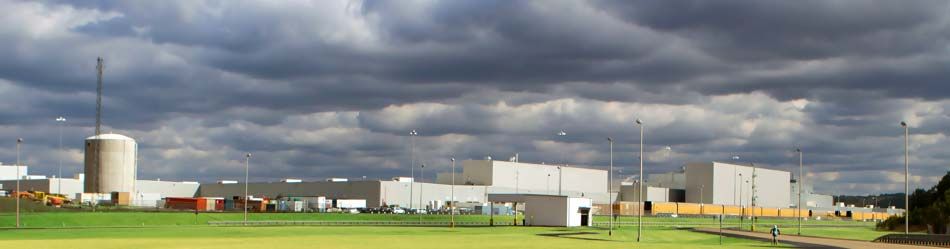
The Body is most of what you see when you look at the vehicle. It consists of the raw metal structure that “surrounds” the passengers. It is also referred to as the “passenger safety cell.” The body parts are manufactured off-site in the form of stamped (pre-formed) sheet metal that are then welded together in separate, close-tolerance, robotic stations to produce sub-assemblies that are subsequentlyprecision-positioned and further robotically combined, aligned, and welded into a metal “shell” that forms the basis of the automobile.
Because of the increased technology in our product today and the complexity of the new products, there is more automation in our plants. We now have over 1650 robots in the plant. Of those, approximately 1250 are in the Body Shop compared to the 85 robots in the original Body Shop. This helps ensure repeatability, consistency, and quality.
The Body shop is divided into separate areas–one for each model manufacturing line: the GLE SUV; GL SUV; and the GLE Coupe. We only have approximately one day’s supply of parts in our body shop- and approximately 40 minutes of parts on the line. Instead of stockpiling the parts next to the Line, our Teams use a computerized push system to order parts to their station as needed. This works by a Team Member pushing a button in their station which then sends a signal to a computerized screen on the forklift. This will tell the forklift driver which part is needed in a specific station.
The welding of the GLE, GL, and GLE Coupe bodies is a precision process. Welds not only hold the components together, they also add safety and overall dimensional accuracy. This dimensional accuracy is very important. It ensures the overall fit and finish of the interior parts which will be installed in the assembly shop. We also use a flexible, non-contact measurement system that uses Laser Sensors mounted on standard industrial robots to measure important dimensional features on parts assemblies. The Perceptron System is a measurement device utilizing highly accurate laser sensors to ensure the dimensions on every body meet the Mercedes-Benz standard of excellence. The Perceptron Systems are multiple laser cameras mounted on robots that measure predefined dimension critical locations through various stages of the production process, ensuring dimensional integrity for the next process.
This data is collected and used by our engineering staff to ensure that dimensional accuracy is being built into the product. This system also provides automatic alarming capabilities and reporting to reduce process variation, and implement process improvements.
The body sections come together in a marriage station where our “PLUS” Computer System “tells” the robots what to do. Every vehicle we produce is for a specific order we have received from one of our 135 countries customers around the world. Once the robots have placed the parts into the framing station, the precision welds marry the under body components together.
We don’t just do traditional welds – we use state-of-the-art laser applications, riveting, screwing, nailing and gluing which are on the leading edge of automotive assembly. We also robotically install lift gates, doors, fenders and hoods in a ‘BestFit’ system which measures the openings with laser sensors and places the components in a position which ensures the tightest gap and flushness control possible.
In a brightly lit area, Team Members perform a final inspection of the body. By using a trained eye to see, and special gloves to help feel the body, they ensure that the body is in perfect shape before sending it to the next station.